What to know about Lean Management
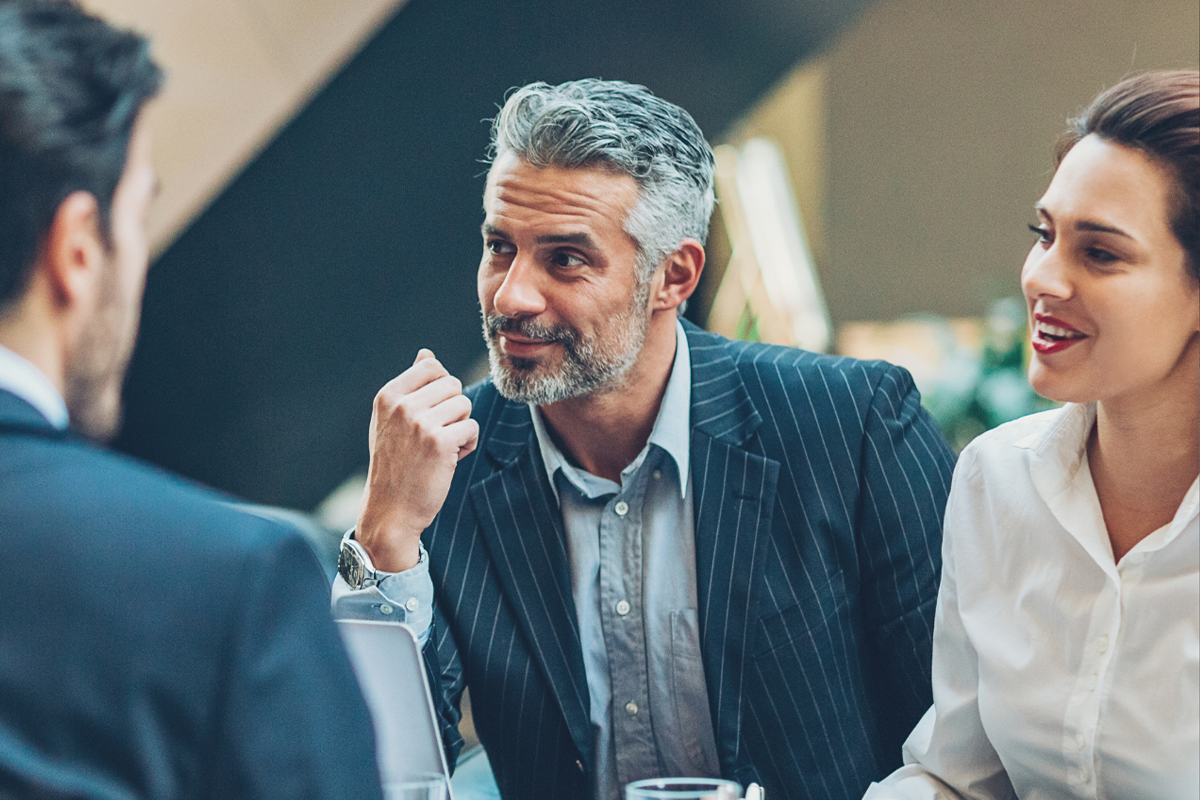
Globalization, political and economic crises, and the accompanying competitive pressures are presenting companies with major challenges. The pace of digitization is also increasing rapidly. These are the reasons why every company should constantly review its business model and adapt it if necessary. How robust is the company in the face of changing external factors?
Optimize and streamline internal processes while reducing costs and focusing on customer value. A key success factor for this is lean management.
This article answers the question of why lean management is essential for competitiveness. What are the core elements of lean management and how can an introduction succeed?
Why you should implement Lean Management
Significance of implementing lean management
Lean management has its origins in the automotive industry. Henry Ford, among others, was one of the pioneers and began the path to efficiency and lean management with the Model T in the early 1920s. The assembly line and production processes were some of the first of their kind to increase efficiency. Then, in the mid-20th century, Toyota became the poster child for lean processes. The company’s practices of efficient use of technology, cost reduction through “just-in-time” inventory strategies, and a holistic production system have inspired companies in many industries.
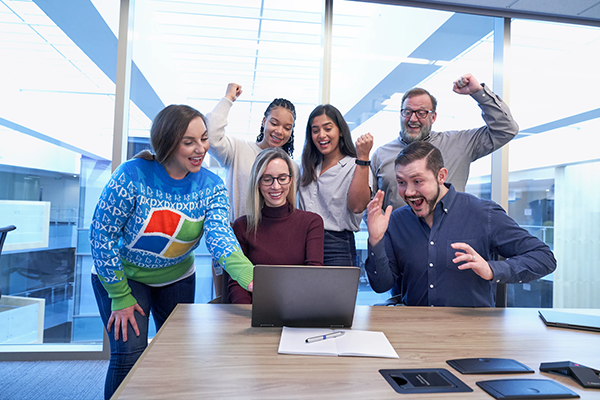
Lean management has helped many other companies succeed after Toyota, regardless of the industry in which they operate. In recent years, lean management has even increasingly found its way into service-oriented industries such as healthcare management, finance, and insurance.
Independent research has found that companies that have implemented lean management have increased deliveries, inventory turns, and productivity by 25 to 33 percent, while scrap and space requirements have decreased by 26 and 33 percent, respectively. Furthermore, in the administrative area, process cycle times have decreased by up to 43 percent. A study by the National Institutes of Health in the U.S. showed results at Virginia Mason Medical Center, which is using comprehensive lean measures. The hospital saw higher profits, fewer deaths, an 85 percent reduction in wait time for lab results and a 93 percent increase in productivity.
So why should you implement Lean Management?
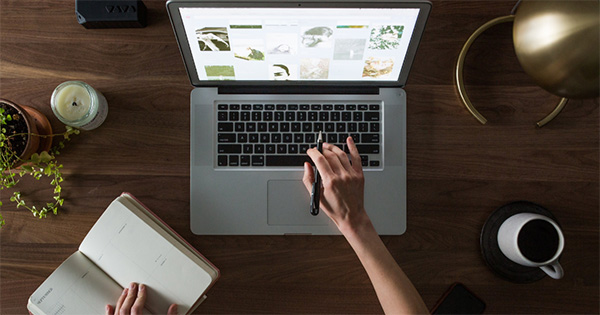
Independent research has found that companies that have implemented lean management have increased deliveries, inventory turns and productivity by 25 to 33 percent, while scrap and space requirements have decreased by 26 and 33 percent, respectively. Furthermore, in the administrative area, process cycle times have decreased by up to 43 percent.
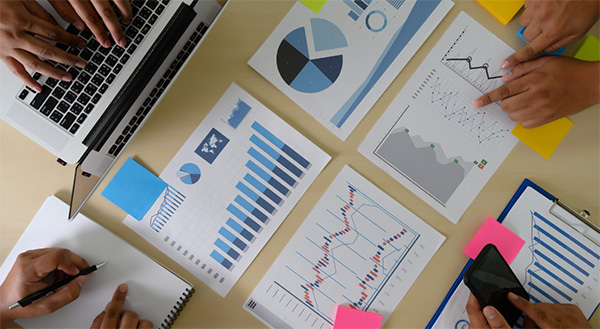
A study by the National Institutes of Health in the U.S. showed results at Virginia Mason Medical Center, which is using comprehensive lean measures. The hospital saw higher profits, fewer deaths, an 85 percent reduction in wait time for lab results and a 93 percent increase in productivity.
To help an organization survive over the long term as it faces new competitors and changing macroeconomic conditions. Properly implemented, Lean management makes a company more flexible and adaptable to change as soon as it occurs (rather than after it has already occurred). Survival gives an organization the ability to better serve its customers over time.
What if the organization has already performed well?
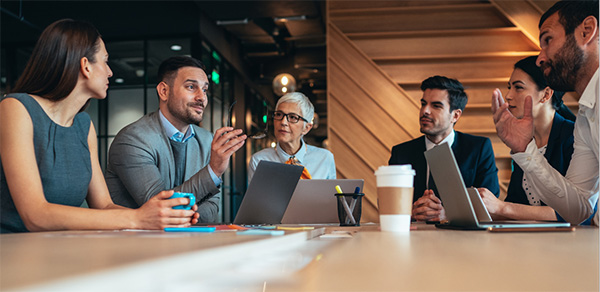
Good performance is relative. Most organizations process essential information using the batch-and-queue method. If that’s all you’re competing with, then your performance may seem good. But customers expect great performance, not good performance. If we are truly customer-centric, then the reason we do lean is to better satisfy customers.
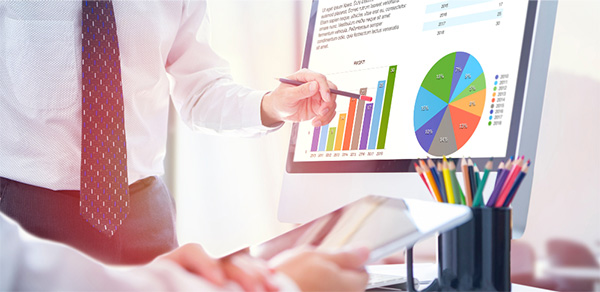
Lean management is a better way to deal with low economic growth that may be with us for some time. Process improvement pays for things a company needs or needs to do for its stakeholders. The benefits will be small and slow to materialize unless leaders recognize lean as a solution to information flow problems, which also improves the health of people in organizations.
For an organization to reap the benefits of Lean management, leaders must admit that all work processes can be improved and that no one is exempt from improvement. An organization in which everyone improves their work processes from the ground up, in a way that does not result in a zero-sum game (win-win), is an organization that will evolve and survive and thrive in the long run.
Create customer value without waste, to streamline and optimize processes and organization. Examples of “waste” include poorly prepared or managed meetings, unnecessary formalities, long multi-step approval processes or overproduction. Incorrect use of technology, unnecessary or excessive reports, and unclear responsibilities also cost a lot of time and lower the motivation of the employees involved.
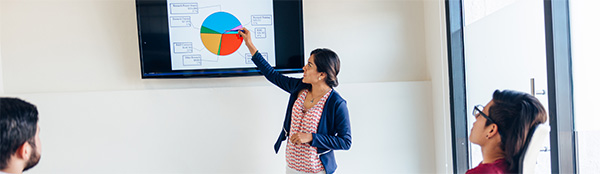
To minimize waste, organizations should focus on the processes that contribute to value creation. Since such a focus saves time and costs, the company can act more efficiently.
What is Lean Management and where does it come from?
Lean management stands for highly efficient work organization that reduces or eliminates everything that is superfluous. Lean management thus encompasses methods, approaches and tools that companies can use to optimize their processes. A company that is lean in this sense focuses on the essentials and uses the right resources at the right time with the right quality to achieve added value for the customer.
It is a recognized management approach that makes it possible to create scope for innovation and for making products more flexible and individual. In essence, it is about using the leanest possible processes to make customer benefits as great as possible.
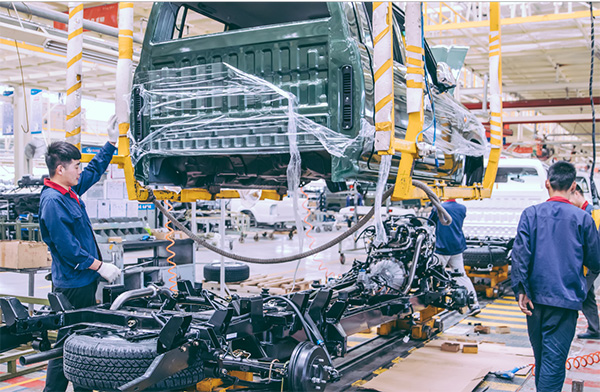
As described above, Lean management is originated in the automotive sector. In the 1980s, Toyota distinguished itself from the competition by its high quality, low scrap and high output with low resource input. The Toyota Production System (TPS) as a management approach stood for lean production of passenger cars. Core elements of the TPS were/are synchronized and standardized processes, the avoidance of errors, improved production facilities and the systematic qualification of employees. Behind this is the goal of continuous improvement.
Regardless of the industry, lean management is about, among other things, providing the customer with a product or service at the desired time, in the required quality and at the best price.
To do this, lean management uses the following four principles:
1. Identify value from the customer’s perspective
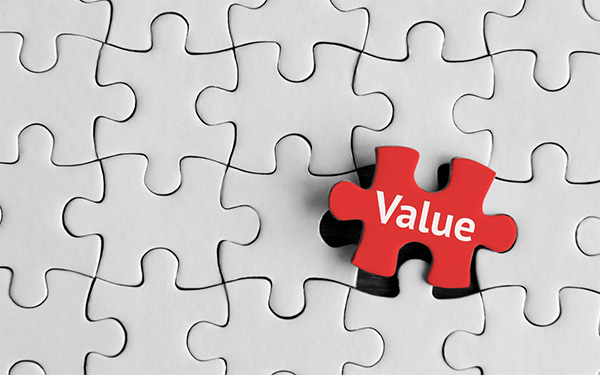
It is about identifying the value stream and getting rid of what is superfluous. The central element for this is the value stream analysis. The value stream comprises all the steps and processes required to manufacture a product or service – from raw materials to the finished product. If only the value-adding processes are considered, wastage or unnecessary functions and also superfluous steps in processes can be avoided in order to improve throughput times. This enables companies to use their resources efficiently and optimally.
2. Flow principle
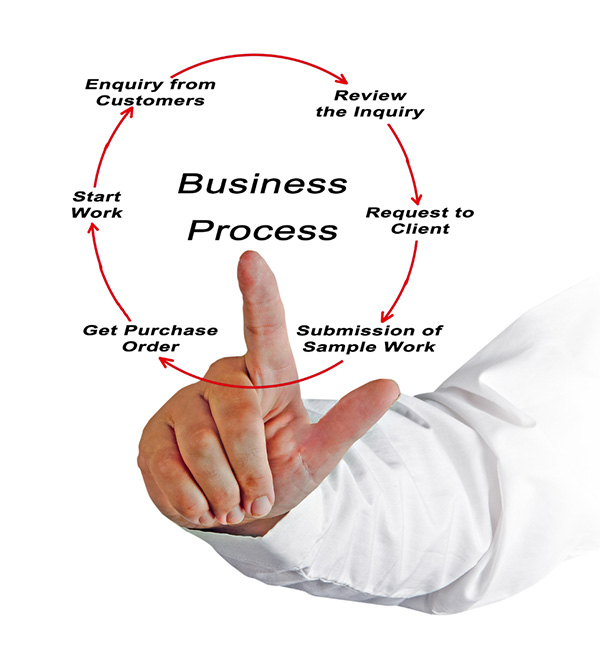
The flow principle refers to a continuous flow of production or business processes in which peak loads and troughs are avoided. In production, for example, this can be achieved by manufacturing in small batches and avoiding idle times and intermediate storage. In administrative processes, it is possible to eliminate inhibiting formalities that delay decisions.
3. Pull principle
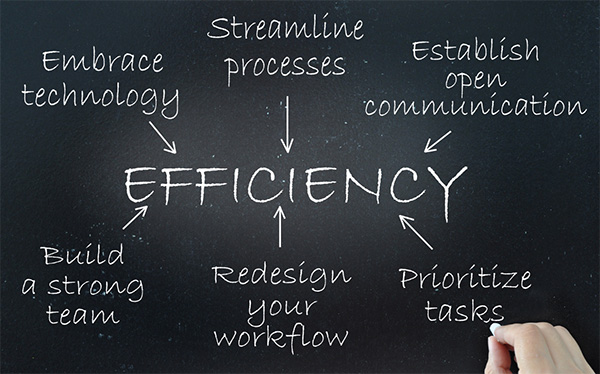
It is about identifying the value stream and getting rid of what is superfluous. The central element for this is the value stream analysis. The value stream comprises all the steps and processes required to manufacture a product or service – from raw materials to the finished product. If only the value-adding processes are considered, wastage or unnecessary functions and also superfluous steps in processes can be avoided in order to improve throughput times. This enables companies to use their resources efficiently and optimally.
4. Zero-defect principle
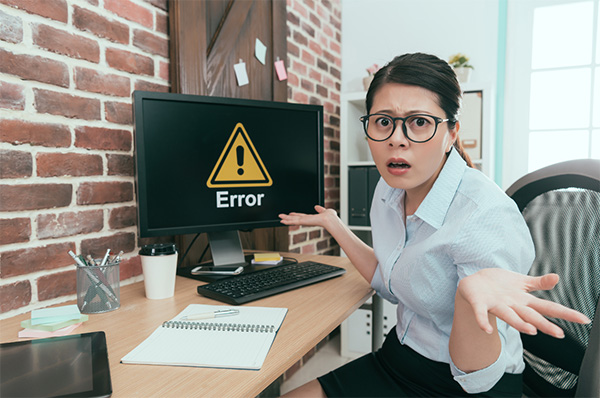
An important principle of lean management is the pursuit of continuous improvement (kaizen) to perfection. Any error is considered a disruption to the process, and managers get to the bottom of problems on the spot and immediately. They look for the causes and eliminate them at the root. The result is an increase in efficiency and quality due to a reduction in errors and an early response to errors, so that error costs are reduced. Companies become a learning organization by permanently identifying and eliminating errors
How to start lean management?
First, the benefits must be considered, i.e., who benefits from the introduction. Both have a benefit from the lean management introduction:
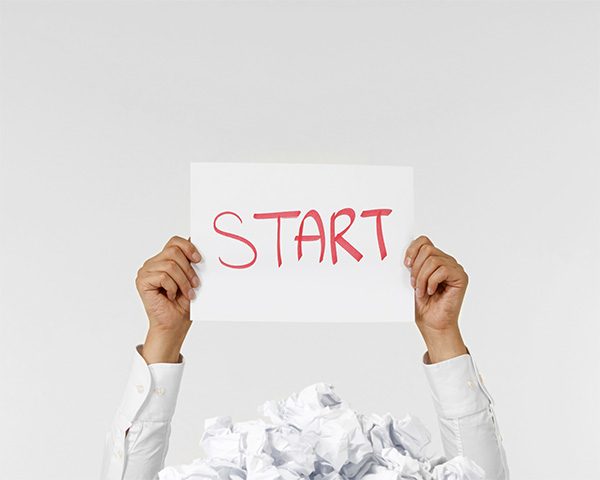
The statement can be illustrated by means of a comparison. Comparing the sales and employee figures of the two automotive groups Volkswagen and Toyota explains why lean management is worthwhile for the company based on personnel costs. In 2017, the VW Group generated sales of around 230 billion euros with approximately 642,000 employees. In turn, Toyota AG generated sales of 228 billion euros with approximately 369,000 employees. Toyota’s profitability is also shown in a 2018 Handelsblatt article. The difference in personnel with almost the same sales can be explained, among other things, by more efficient, or less wasteful, processes.
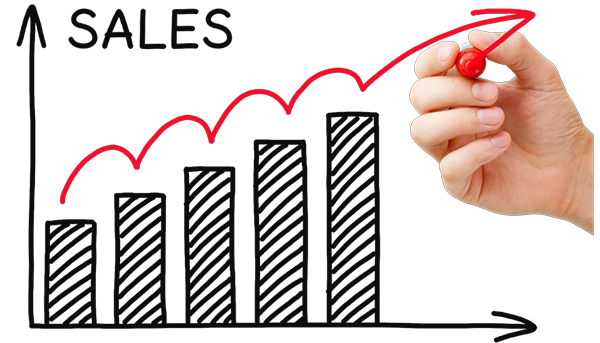
Lean management is both a set of methods and a philosophy and is therefore holistic. Employees are the key to success. If the company adapts the Lean Management philosophy and adapts it to its own culture, the employees are challenged and encouraged. Through resulting improvements, the freed resources will be put on new projects to further increase competitiveness.
This means that in order to introduce Lean Management, it is not enough to make individuals in the company “responsible” for implementing the measures. Management must drive the issue and stand behind it.
As a first step, we recommend on-site training with methods tailored to the company and its needs. The second step is to anchor Lean Management in the organization. Here, departmental managers are appointed and trained. These then start to implement it in the respective work area. In an iterative process, we look at how the use of the tools affects the performance of the departments and, if necessary, make adjustments.
From experience, we recommend the 6S approach for the introduction of the first methods. This ensures that all employees are involved and that the first successes can be shown quickly.
What are the challenges and pitfalls?
The basic idea of lean management combines fast problem solving with continuous improvement. It is important to be honest, to analyze the actual situation relentlessly and to make the problems visible instead of hiding them. This only works in a corporate culture that does not condemn mistakes but sees the recognized shortcomings as an opportunity for further development and improvement. Here, many companies still have some catching up to do.
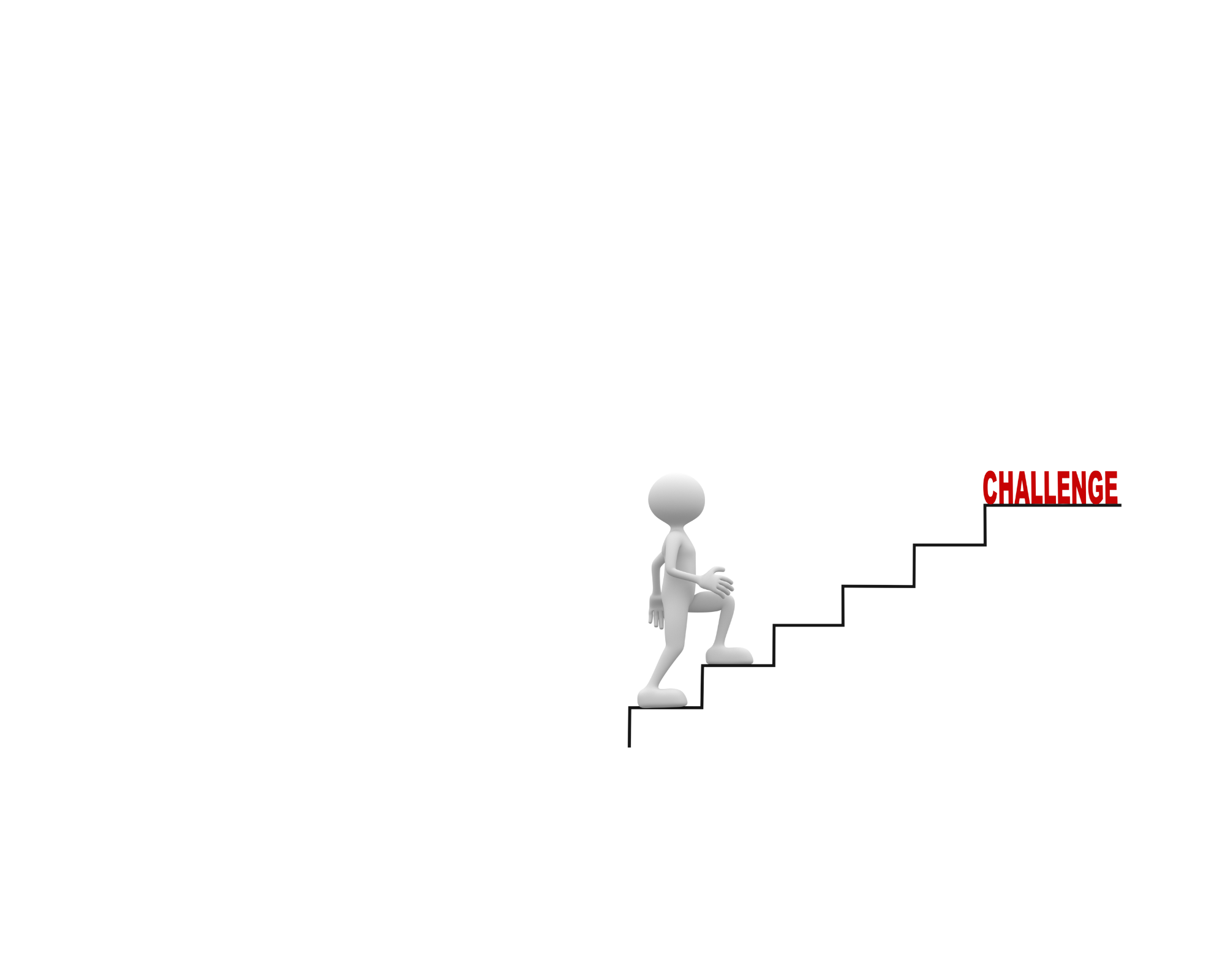
Since value stream mapping covers all manufacturing processes from raw material to finished product, companies must also take a cross-departmental and cross-organizational approach. Silo structures in areas such as purchasing, sales or production sometimes make this difficult. The prerequisites for success are open communication, a move away from departmental thinking and, in some cases, the overcoming of strong hierarchies. An elaborate, strongly controlled change process is necessary. The change will only succeed if the management is fully behind lean management and all employees in the company