What does 6S mean in businesses?
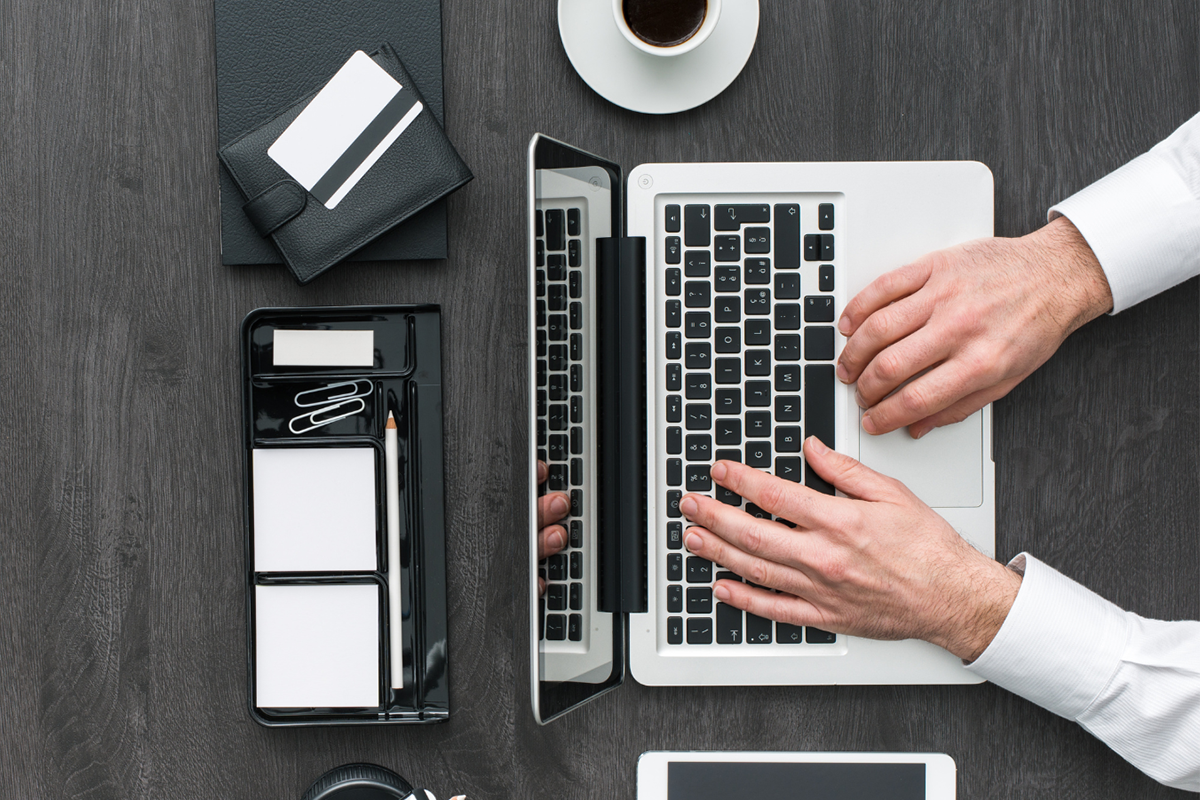
In today’s business environment, flexibility and robustness in the face of changes in the market are the keys to long-term success. In addition to strategic alignment, companies must constantly look at how they can make their business processes more efficient, continuously improve, and avoid waste.
Why should you use 6S in your organization?
Successful companies therefore rely on lean management as one of the cornerstones of their management system. While Lean Management as a business system originally came from the productive environment at Toyota Motor Corporation, in the last 15 years more and more companies have recognized that the methods and tools of Lean Management must also be applied in the more administrative environment, as there is a lot of potential for increasing efficiency here.
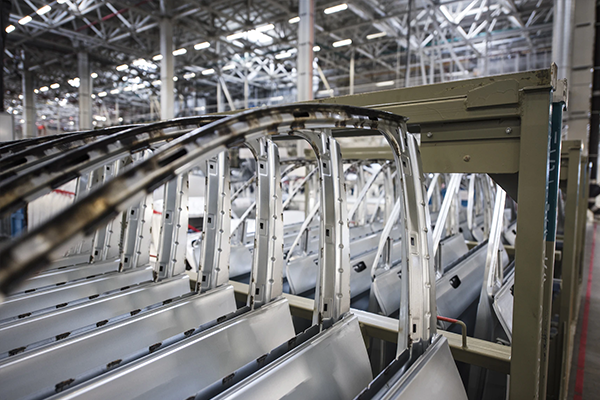
6S has its origins in a method called 5S, which was developed by Toyota in the mid-20th century as part of the Toyota Production System (TPS). The TPS, with its tools, enabled the Japanese company to produce higher quality products faster, with less waste and lower inventories than its competitors. While these fundamentals were created many years back, the benefits of the methodology withstand even in today’s conditions.
The methodology 5S literally stands for 5 individual S-words, namely sort, order, shine, standardize and sustain. Successful implementation of the 5S process serves to remove unnecessary items, clean space, reorganize, develop procedures, and improve discipline. 6S is the next evolutionary stage of the 5S method. The 6th S stands for safety.
Implementing the 6S method throughout the company has several benefits:
1. Increased productivity in all departments.
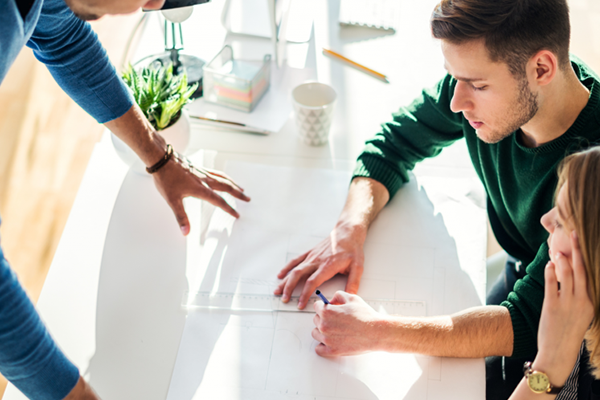
Every company strives to increase the productivity of its business processes because productivity increases the overall return on investment. According to global research conducted by various consulting firms in the U.S., it has been determined that effective implementation of the 6S method enables this improvement.
Consistent elimination of unnecessary items and materials combined with efficient maximization of workspace is enough to increase productivity with minimal wasted time. Less time spent searching for unnecessary items means more time for value-added work.
2. Improved safety
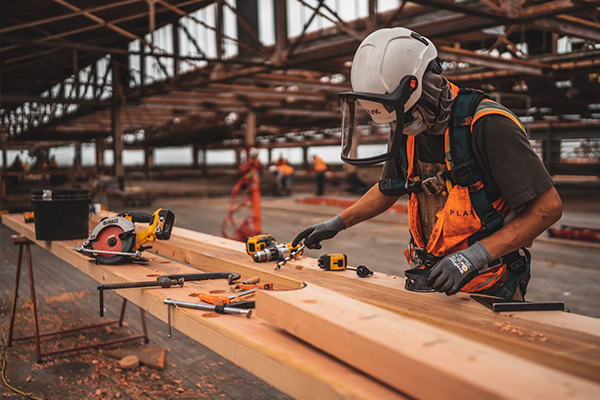
Improved safety is another benefit of 6S implementation. A clean workplace environment, especially in a production unit, will result in a significant reduction in the number of accidents or near misses.
Often, unattended spills of liquids increase the risk of slips and falls. In contrast, following standardized cleaning procedures will limit the possibility of such preventable incidents. Reducing unnecessary travel through the work environment also minimizes the risk of injury by limiting exposure to hazardous materials elsewhere in the facility. This, in turn, boosts employee morale as the reduction in injuries demonstrates the employer’s concern for employee safety.
3. Reduction of Waste
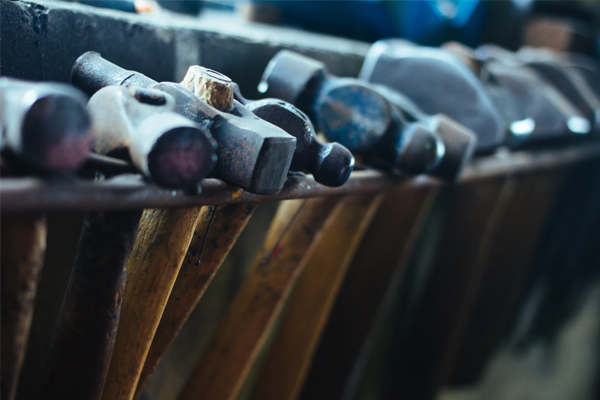
The implementation of 6S also results in a significant reduction in lost walked or damaged items in the workplace.
A clear and orderly workplace with proper labeling gives employees the flexibility to replace damaged items in their designated locations, minimizing the overall number of misplaced and lost tools and equipment. In addition, proper equipment management also minimizes the damage that generally occurs to various parts of the products during the production process.
4. Employee Engagement
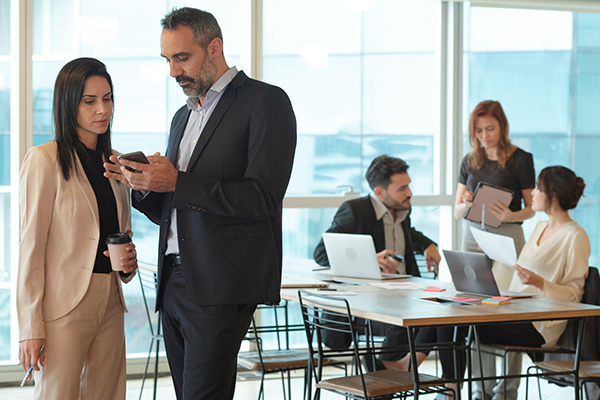
By implementing 6S in the company, employees are responsible for applying it in their own work area. 6S emphasizes on employee engagement by giving them the opportunity to contribute to make productive changes to the overall design of the workplace and to perform maintenance tasks.
This encourages worker participation for long-term sustainability of the workplace, which in turn increases their commitment to the work. This improvement also has the side effect of decreasing absenteeism in the workplace.
What are the steps of 6S?
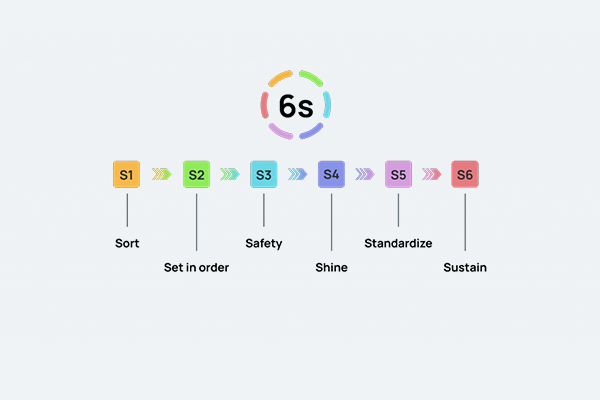
Lean Management with all its tools and methodologies seeks to cut costs, increase employee satisfaction, and cut down on waste by tightly managing and organizing every aspect of the business process — ultimately incorporating concepts like keeping tools visible and workspaces clean, and giving workers a sense of autonomy and involvement. The methodology spread throughout Japan, then hit the U.S. and spanned worldwide starting in the 1980s.
The 6S concept by itself, whose steps are mainly concerned with creating a tidy work area, identifying and storing items that are most frequently used in production, and maintaining that orderly system. Here’s a summary:
The 6S concept is based on these six steps:
Sort - Sort out unneeded items
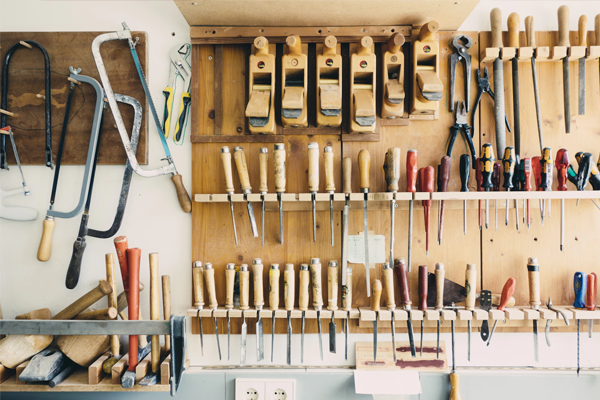
The first step is essentially: Get rid of anything unnecessary that isn’t used on a regular basis. Basically, anything that doesn’t bring joy – or in this case, utility – to the factory floor or office. The following steps make the difference between 6S and make it a useful tool of a broader theory known as visual control, which essentially says that systems are more efficient when all of their elements are visible and easily accessible.
Straighten - Have a place for everything
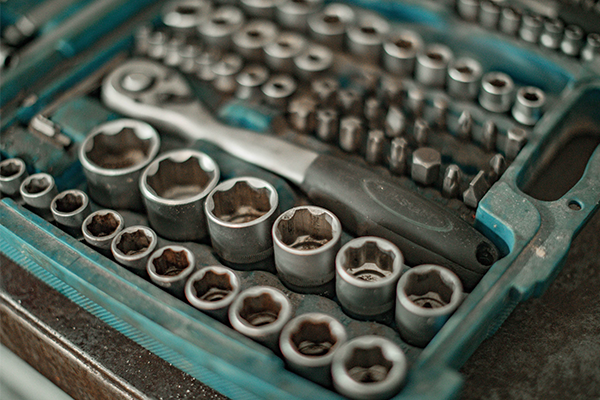
It’s time to do this after deciding which items you should keep, move, or discard. Workplace setup should be as practical as feasible.
Equipment that is often utilized should be easily reachable by employees. Remember that goods being stored shouldn’t restrict movement or present hazards to personnel (e.g., stock stored in heights without fall protection).
Safety - Keep the area safe
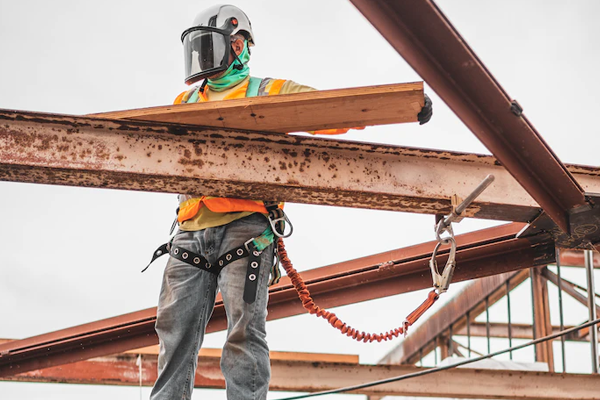
Safety as one independent step, which anchors on ensuring workplace safety and risk assessment. With safety, as one S, managers can work on minimizing short- and long-term hazards which are detrimental to the physical and mental health of employees. When the workplace affords employees a sense of safety, it also leads to improved focus and lower stress levels.
Shine - Keep the area clean. – That simple!
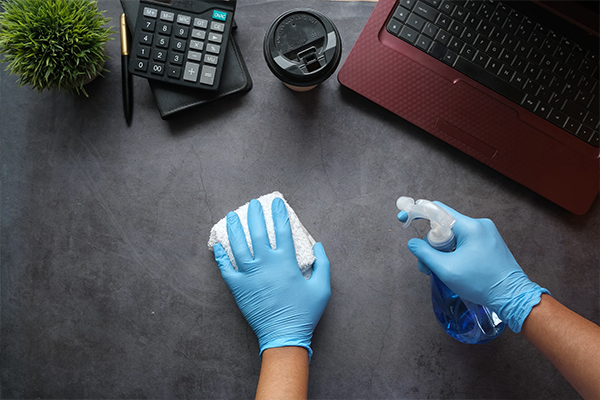
In the following phase of the 6S lean management principle, make the workplace “shine.” It’s time to conduct a thorough cleaning to make the space organized and tidy.
To make sure that cleaning is not just a one-time event, but a typical procedure followed moving forward, you should establish a regular cleaning schedule.
Standardize - Create rules and standard operating procedures
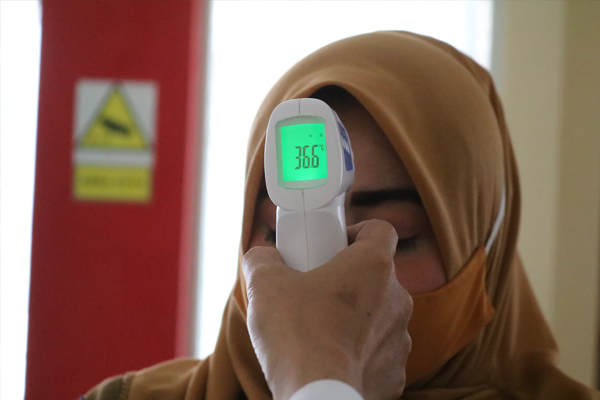
Once everything is clean and in its right place, that becomes the standard–meant to be maintained every day.
The fifth stage of the 6s method, “Standardize,” aims to create a new standard for the workplace by identifying best practices and developing standardized procedures for the first three phases. It tries to assist individuals in creating consistent work patterns across their processes and forming more productive habits. Visualizations, defining worker responsibilities and duties, routine examinations, and frequent site audits can all help with this.
Sustain - Maintain the system and continue to improve it.
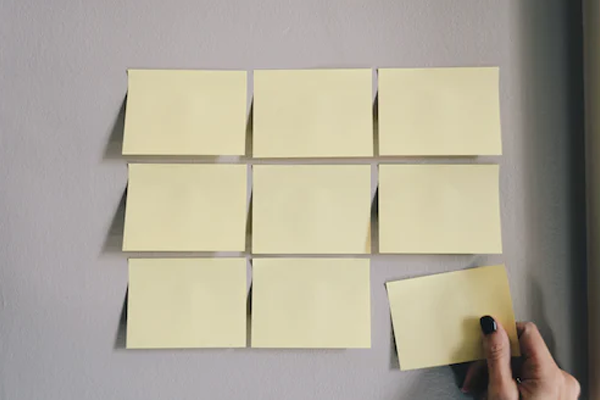
The purpose of this stage of the 6S technique is to establish the standardized procedures are consistently applied over a lengthy period of time until they become part of the day-to-day work routine.
The concept also relies on the self-discipline of employees to maintain the proper order systematically, without being told. In that way, tidying up becomes a routine—a series of tasks that are almost second nature. And those milliseconds saved in not searching for a tool or having to clean it before use turn into monetary gains.
How could you implement 6S in your business?
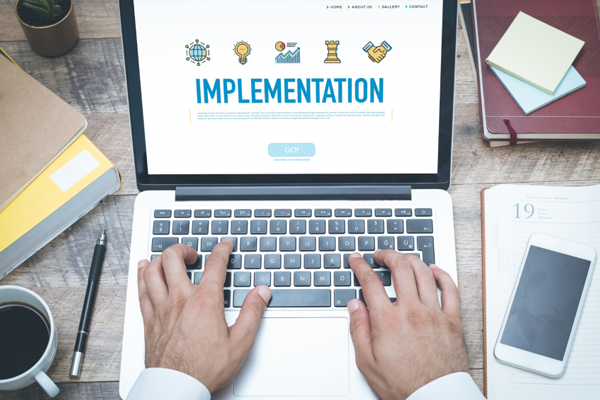
As stated, implementing 6S can lead to several important benefits, and companies use the methodology to solve some of the most critical pain points.
Before you get started, let’s perform a test. If you answer yes to most of the following questions, you will find 6S useful and effective:
- Do people in your workplace struggle to locate documents or files, whether in physical or digital format?
- Are there loose, sagging electrical cables in the workplace?
- Are there files, drawers, and cabinets that are unlabeled, or do they contain unmarked content that is hard to identify?
- Is valuable space taken up by useless items?
- Are there papers in your workplace that are not used and are gathering dust?
- Does everybody know how to keep the workplace organized and are fully aware of their roles and responsibilities?